Neben der Auswahl des Gehäusedesigns hat die Ausführung des Innenlebens maßgeblichen Einfluss auf den Nutzwert eines Produktkoffers. Im Idealfall erfüllt es nicht nur Schutz- und Ordnungsfunktionen, sondern unterstützt zugleich die Usability und Ergonomie des Inhalts. W.AG bietet deshalb eine große Bandbreite an verfahrens- und materialtechnischen Möglichkeiten zur Realisierung passgenauer und anwendungsfreundlicher Inlays.
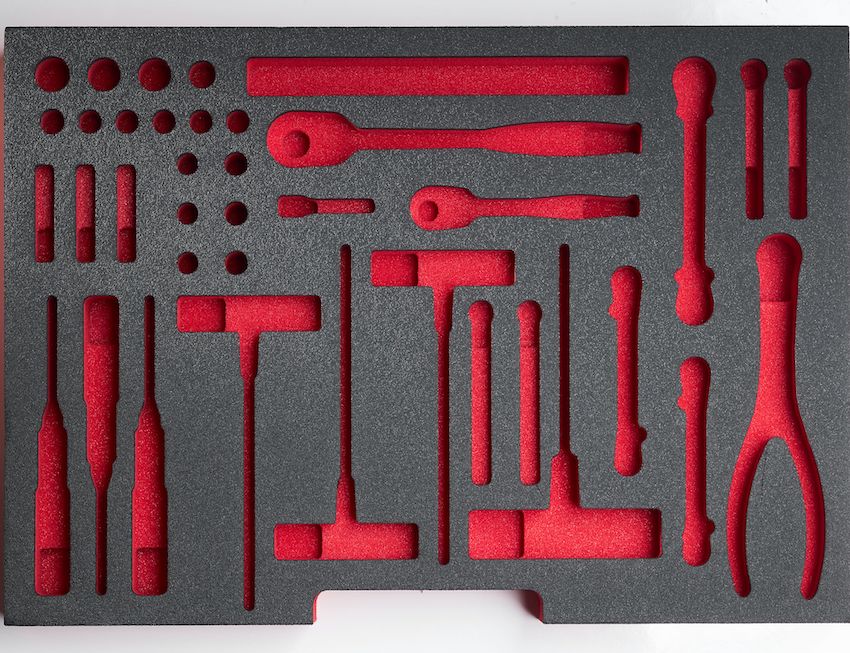
Vor einigen Jahren bereits hat der deutsche Kofferhersteller W.AG die Werte Nachhaltigkeit und Ressourcenschonung als Leitmotive für die Realisierung seiner Produkt- und Präsentationskoffer definiert. Das gilt sowohl für die Gehäuse, die derzeit in drei umweltschonenden Werkstofflinien produziert werden, als auch für die Fertigung der geometrisch mitunter überaus komplexen Inlays. Während die Halbschalen und Verschlüsse der Koffer in großen und kleinen Serien in einer der mittlerweile 23 Spritzgießmaschinen zu ihrer Form finden, nutzt das Unternehmen in der Inlay-Fertigung neben dem Wasserstrahl- und Laserschneiden auch das Präzisionsstanzen und das CNC-Fräsen. Konzentriert sind alle diese Kompetenzen am Firmenstandort Geisa in der Rhön.
Dank dieser verfahrenstechnischen Bandbreite ist W.AG in der Lage, schwarze, graue und farbige PU- und PE-Schaumstoffe in unterschiedlichen Härtegraden und Dichten in kundenspezifisch konfektionierte und passgenaue Koffereinlagen zu verwandeln. Zudem stehen über die Auswahl dieser konventionellen Schaumstoffe hinaus inzwischen auch besonders nachhaltige Schaumstofflösungen zur Verfügung, mit denen sich ebenfalls präzise, feste, sterile und wasserabweisende Inlays fertigen lassen.
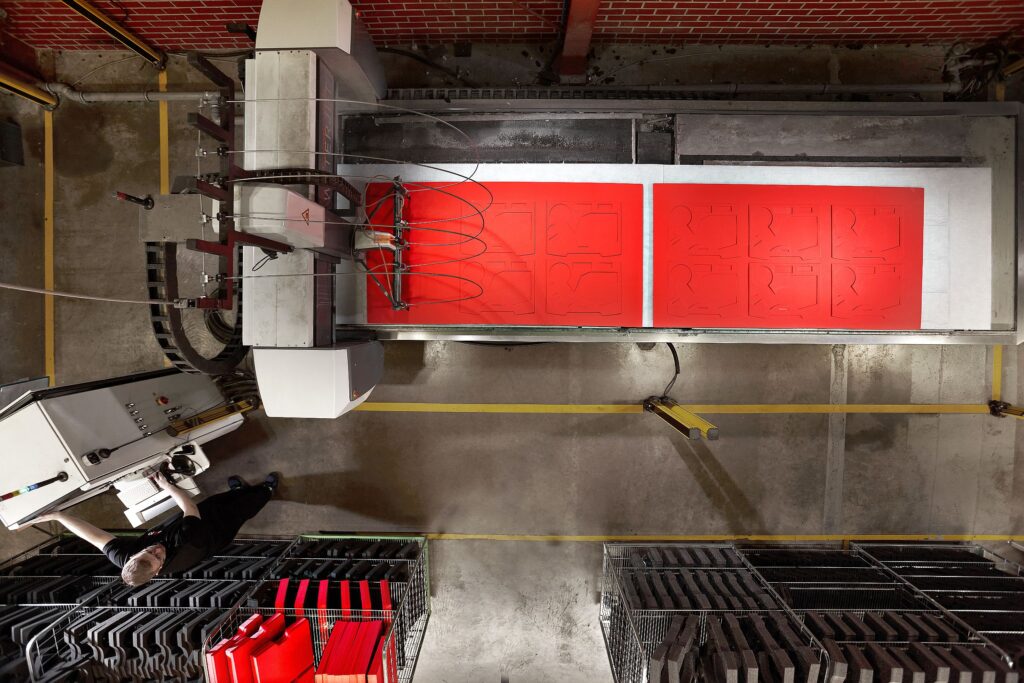
Konkret heißt das, dass all jene Kunden, die den ökologischen Fußabdruck ihrer Produkte und Marken konsequent reduzieren wollen, aus aktuell zwei Alternativen auswählen können. Denn zum einen vermag das Unternehmen in seiner Werkstofflinie Organicline nachhaltige Kofferlösungen zu realisieren, die innen und außen aus einem ressourcenschonenden Bio-Compound bestehen, das zum großen Teil aus nachwachsenden Rohstoffen gewonnen wird. Und zum zweiten hat es vor wenigen Monaten die Werkstofflinie Circleline ins Leben gerufen. W.AG verarbeitet hier gemäß den Vorgaben des European Green Deal für die Kofferschalen bis zu 30 Prozent recyceltes PP aus Post Consumer- und Post Industrial-Kreisläufen, während für die Inlays ein Schaumstoff mit mindestens 30 Prozent recyceltem Polyethylen zum Einsatz kommt.
Sämtliche Alternativen, die W.AG seinen Kunden auf dem Gebiet der Inlay-Fertigung bietet, lassen sich mit allen drei Werkstoff-Linien und allen sechs Kofferlinien des Unternehmens kombinieren. Produktentwicklern, Marktstrategen und Herstellern eröffnen sich damit viele Möglichkeiten für das Design ihrer Verpackungen, Transportbehälter und Aufbewahrungsmittel. Insbesondere Firmen, die ihre Produkte mit nachhaltigen und ressourcenschonenden Store-and-Use- und Green Packaging-Lösungen aufwerten möchten, finden in W.AG einen kompetenten und flexiblen Projektpartner für ihre Ideen.